OTA Firmware Updates in IoT: Challenges, Realities & Best Practices
- Eurth Engineering
- Jul 15
- 4 min read
Estimated Reading Time: 10–15 Minutes
Author: Vijay Kumar Sanugondla, Embedded Engineer at Eurth Techtronics.
In the connected world of smart devices, Over-The-Air (OTA) firmware updates are no longer a luxury — they are a critical foundation for long-term value delivery. From security patches and compliance updates to performance improvements and feature rollouts, OTA enables connected devices to evolve post-deployment — without ever touching the hardware.
At EurthTech, we engineer embedded and IoT platforms that live in the real world — where networks are unstable, power is limited, and scaling to 100,000+ devices requires bulletproof strategies.
In this blog, we explore the technical, operational, and business-critical aspects of OTA, share best practices, and offer real-world insights from projects where OTA made — or saved — the product.
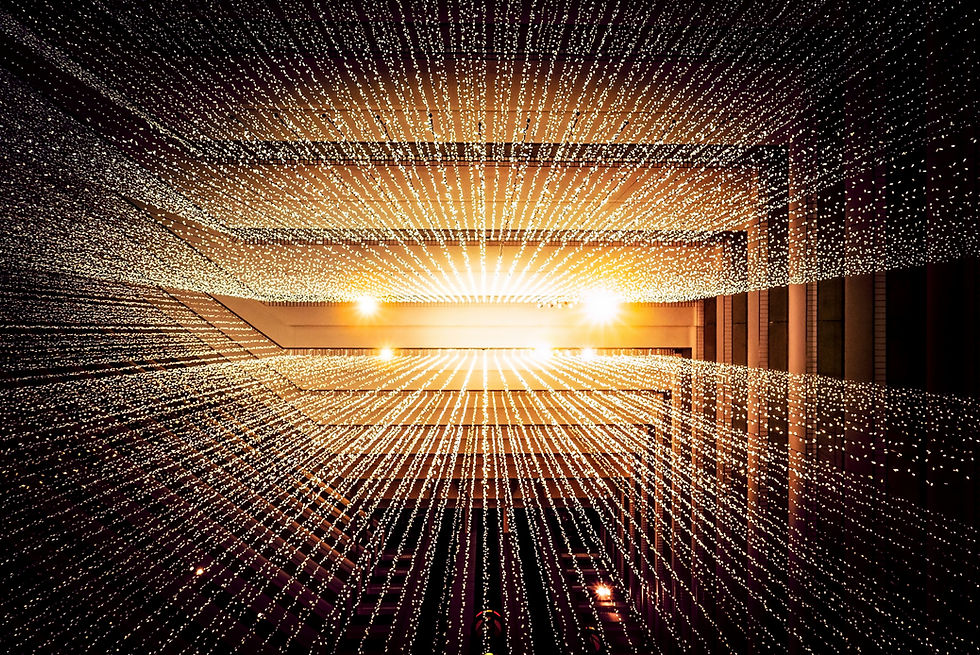
1. Why OTA is Mission-Critical in IoT
In many connected device ecosystems — from agricultural sensors to industrial gateways — physical access for firmware updates is either impractical or impossible.
Here’s what OTA enables:
Security Patches — Fix CVEs and critical vulnerabilities quickly
Feature Delivery — Add capabilities post-deployment
Compliance — Respond to evolving certifications (e.g., Matter, IEC, FDA)
Cost Reduction — Avoid truck rolls, manual service, or product recalls
Case Study: A smart water metering solution deployed in rural zones needed a critical time-sync patch. Without OTA, over 20,000 units would’ve required manual intervention — delaying compliance and increasing operational costs.
2. Anatomy of a Robust OTA Framework
An effective OTA system must be secure, resilient, and cloud-integrated, with components on both the device and the backend:
Component | Function |
Update Server | Hosts firmware, manages rollout policies |
Bootloader | Handles validation and safe flashing of updates |
Update Agent | Periodically polls or receives push triggers |
Rollback System | Ensures recovery on failure (e.g., bad flash, power loss) |
Telemetry + Logs | Captures status, errors, and update metrics |
3. OTA Challenges in Real-World Deployments
Designing for OTA isn't just about pushing a binary. It’s about dealing with real-world constraints in hardware, networks, and deployment logistics.
a. Unreliable Connectivity
Challenge: Interrupted downloads over patchy networks (e.g., LoRaWAN, NB-IoT)
Solution: Use resumable downloads, multi-part retries, or delta updates
b. Firmware Security
Challenge: OTA can be an attack vector if not protected
Solution: Use digitally signed binaries, TLS transport, and secure boot
c. Power and Memory Constraints
Challenge: Low-power MCUs often lack staging memory
Solution: Use A/B partitions, external flash, or compressed updates
d. Bandwidth Cost
Challenge: Cellular/MQTT/LoRaWAN updates can be slow and expensive
Solution: Use differential patches (e.g., bsdiff) and regional caching
e. Version Compatibility
Challenge: Firmware might break cloud APIs or hardware variants
Solution: Build in backward compatibility, feature flags, and version handshakes
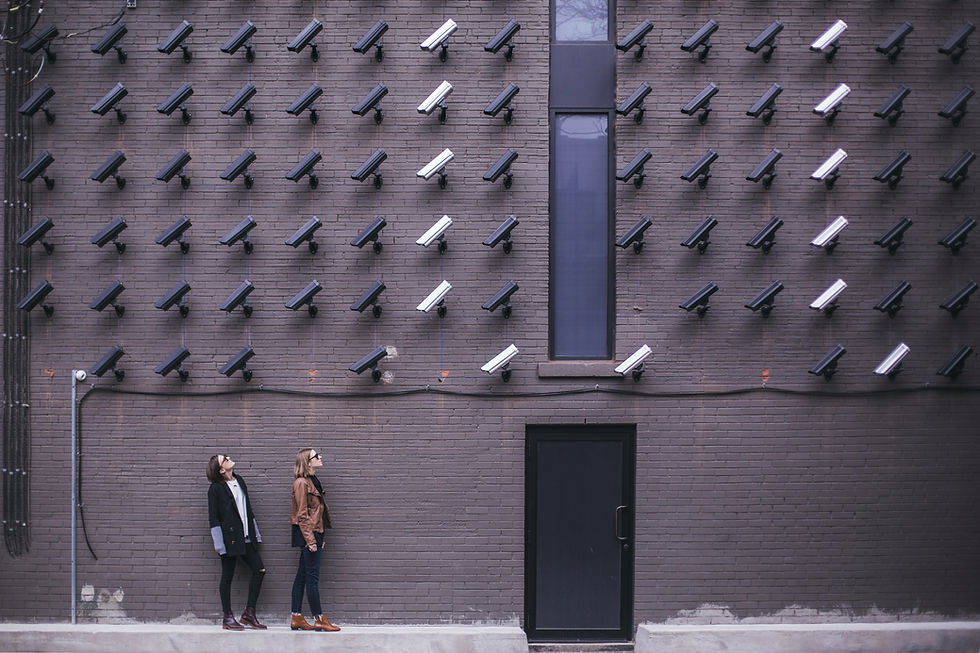
4. A Secure OTA Lifecycle: Step-by-Step
Building trustable OTA means designing for cryptographic assurance, failure recovery, and infrastructure scaling:
Firmware Signing – Each release signed with private keys
Cloud Distribution – Served via authenticated endpoints (rate-limited)
Device Authentication – Mutual TLS or device certs for validation
Download + Verify – Secure hash check before applying
Fail-Safe Apply – Bootloader supports rollback if update fails
🔐 Security by design, not by patch.
5. Battery-Powered Devices Need OTA with Constraints in Mind

Low-power devices (e.g., wearables, agri sensors) introduce OTA complexity due to:
Sleep cycles and missed updates
Energy cost of downloads
Limited RAM/Flash for staging
Design Tips:
Trigger checks during scheduled wake-ups
Use compressed OTA formats (e.g., heatshrink, LZMA)
Opt for broadcast of availability, not payload
File systems like LittleFS reduce flash wear
Example:In an NB-IoT soil moisture sensor, OTA using heatshrink compression reduced energy cost by 40%, enabling longer battery life without compromising update agility.
6. Test Before You Regret: OTA Validation Essentials
A faulty OTA rollout can brick thousands of devices — a nightmare for both engineers and business owners.
Your validation pipeline should simulate:
Power loss during flashing
Signature tampering scenarios
Rollback triggers
Hardware variants & flash sizes
Use CI pipelines, hardware-in-loop testing, and field trials before wide rollout.
7. Real-World Examples from the Field
Smart Speaker — Audio Sync Bug
Problem: Regional audio delay
Fix: 8KB delta patch OTA to 1M+ units in 48 hours via staged rollout
Industrial Gateway — CVE Mitigation
Problem: Vulnerable SSH stack discovered post-deployment
Fix: Signed binary patch pushed over MQTT, validated via telemetry
Medical Device — Bluetooth Cert Update
Problem: Spec change for BT advertising
Fix: OTA pushed firmware-level control; validated across SKU matrix
8. OTA Best Practices: Quick Reference
Sign firmware and verify before flashing
Prefer delta over full-image updates
Design for rollback (A/B or dual-bank)
Simulate OTA failure cases
Encrypt transport and storage
Log update metrics and errors
Maintain cloud compatibility versioning
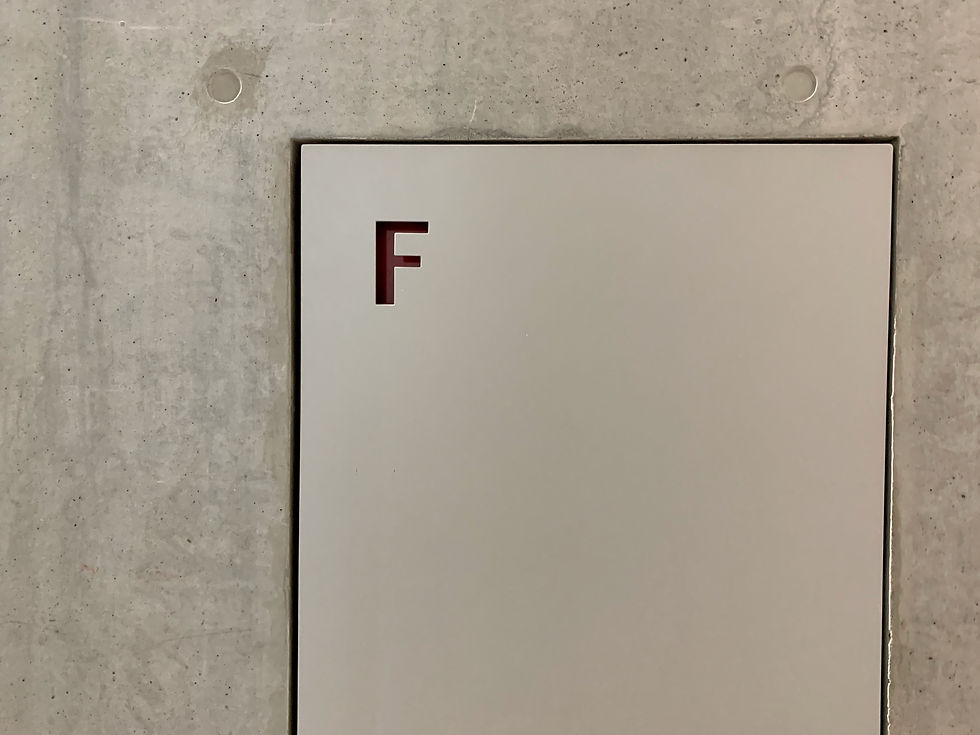
Conclusion: OTA is Not a Feature — It’s a Responsibility
As connected products scale, OTA becomes a core requirement for reliability, security, and business agility. But implementing it correctly takes more than just cloud storage and firmware flashing.
At EurthTech, we design OTA systems that are resilient, secure, and power-aware — and we help our partners scale confidently, knowing that their devices are ready for what’s next.
Thinking about building a robust OTA pipeline for your embedded product?Let’s connect — Contact EurthTech
Comments